Pressure Guard
Pressure Guard
On January 1, 2019, SAF Holland purchased a controlling interest in Pressure Guard.
If you own a Landoll or any other brand trailer with a problematic Pressure Guard system, we offer retrofit kits to solve the axle leak issues. Please give us a call and we’ll walk you through what’s required. We are well experienced with the Pressure Guard issues.
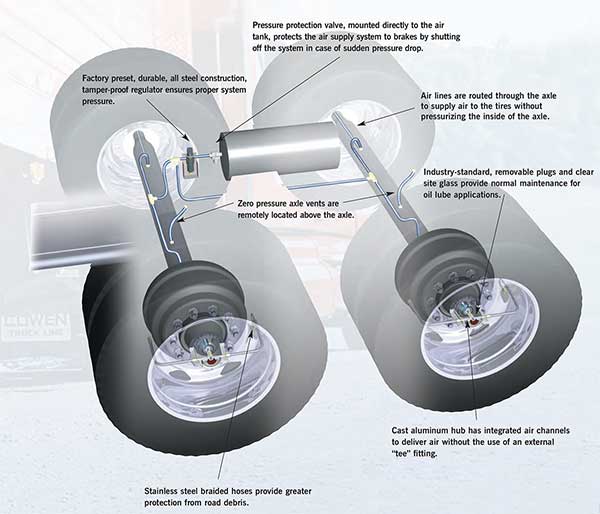
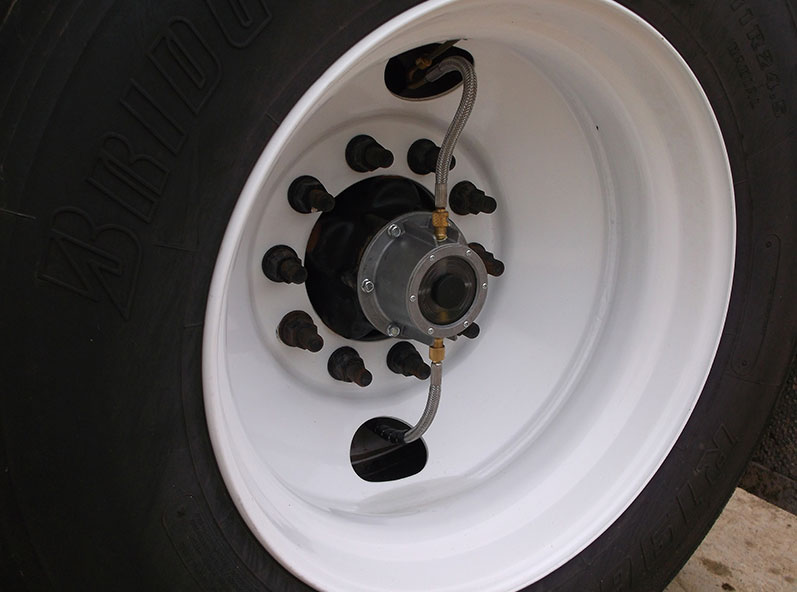
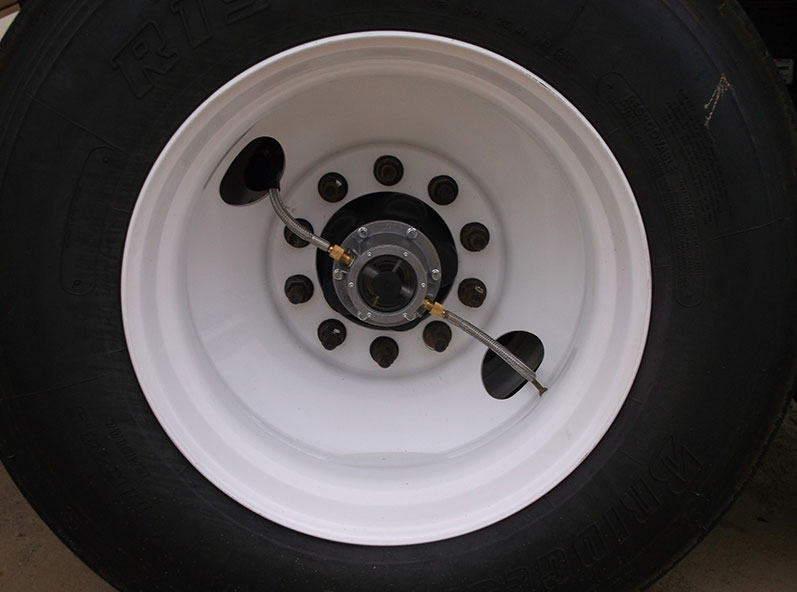
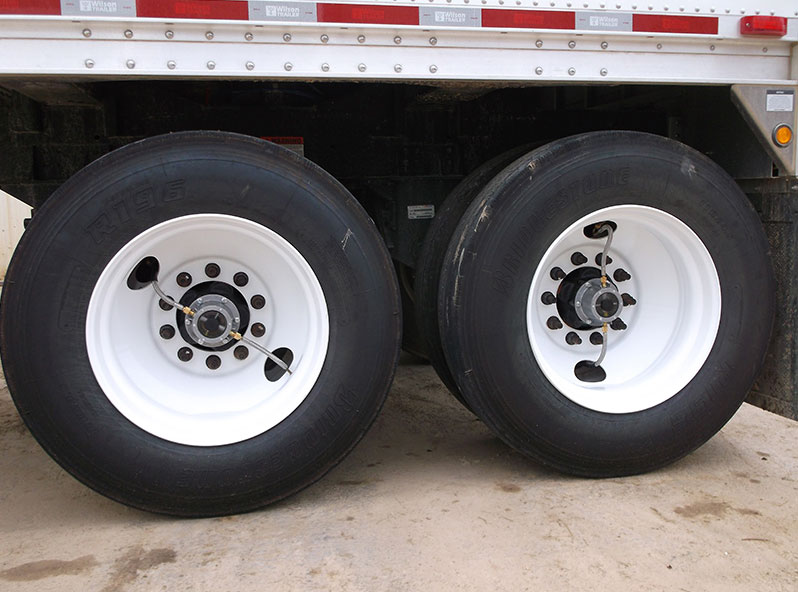